Ah, yes! Today it’s been amazing! Days like this is what you dream of in the winter time, where the sun keeps you warm until it is just about to set after nine o’clock, having a full day of sunshine and a nice breeze.
This weekend I got some more neighbors temporarily. I heard some mooing as I was doing some research in the boat and when I peaked out of the companionway these fellas looked back at me. Cows are funny! Later in the day I could hear a man shouting and I popped my head out to see what was happening this time. He was calling the cows and they all came to meet him at the gate, and as he opened it they started walking back to the farm. It was time for milking.
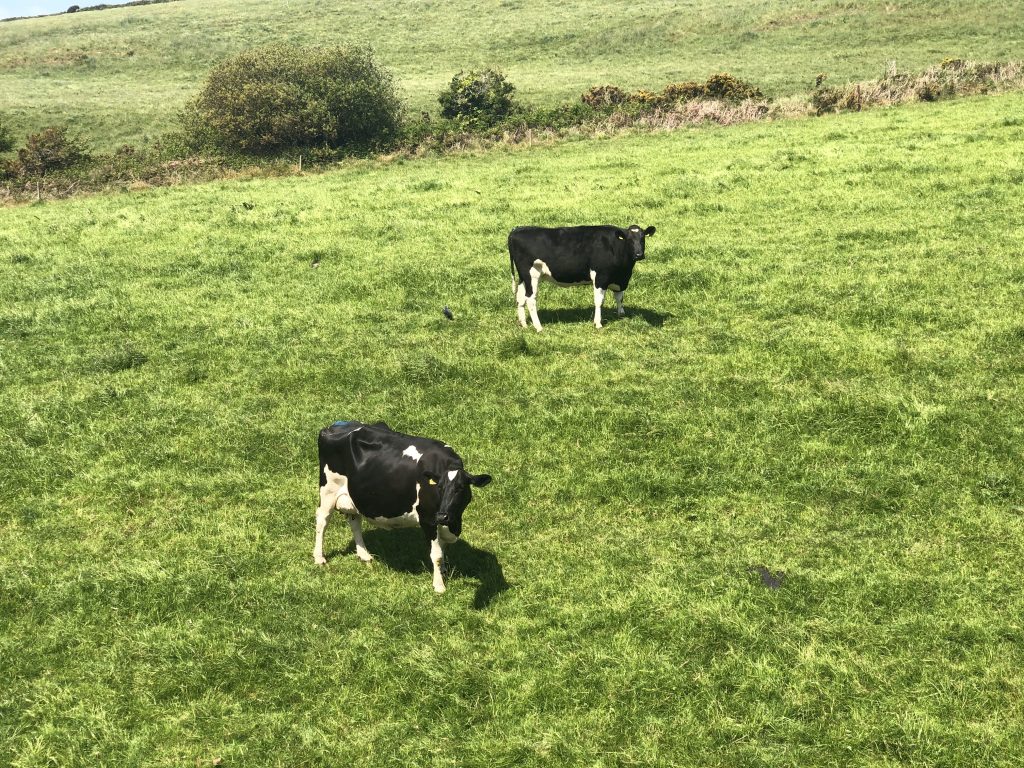
What I was doing when I got interrupted by this beautiful picture? Well, I’ve finally been playing around a bit with my Weimo D1 mini clones. The idea is to use them to make it easier to control lights, fans and such by changing switches to momentary buttons where needed and then add some home automation wizardry to make the buttons “smart”. As an added bonus I can use my phone to control them as well, if I want to.
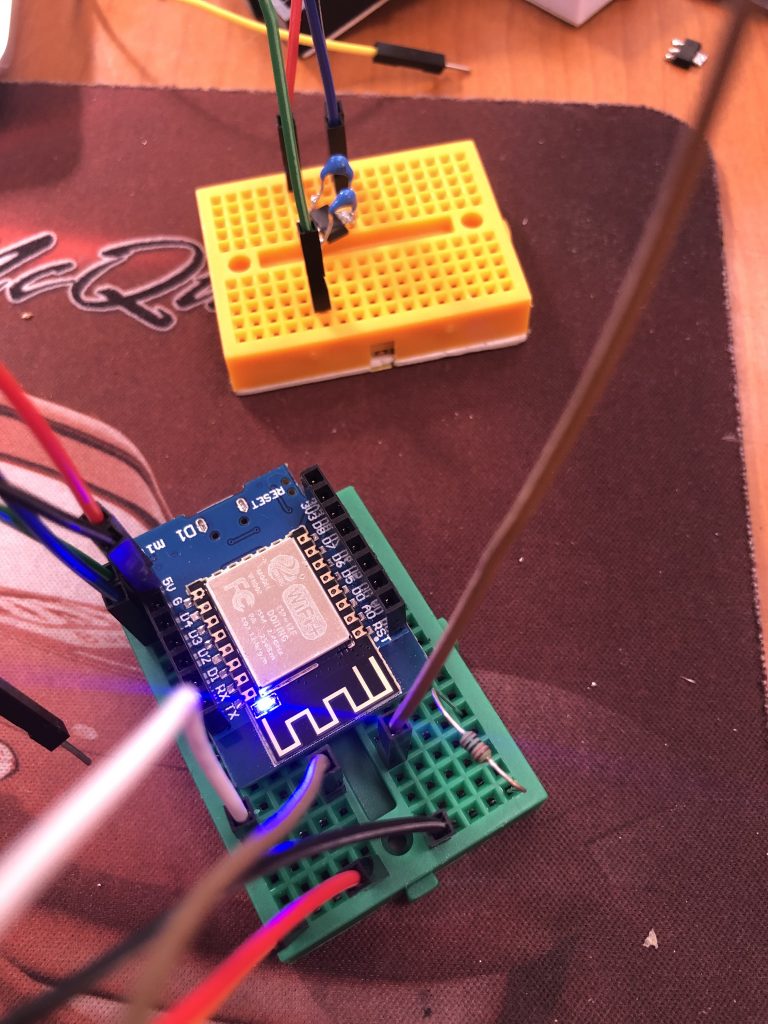
First hurdle to get pass was to figure out how to run a 5V mini computer in a 12V system. I have been ordering some electronic components and one was a tiiiny component (up in the top right corner) that turns 16V, or lower, to 5V. I did need a pair of capacitors to get it to work, but it does (on yellow breadboard). Very sweet! The only thing is that I’ve been watching some YouTube videos of a guy automating an DIY RV and he obviously did a better research job than I did and showed some tiny boards with all this on, well waddayaknow, they obviously sell small boards that does this specific task. Well, now I know. Or, I did they existed but I wanted to go full DIY with it. But the guy had a really good argument not doing it: standard components are usually very easy to replace and substitute as they break down. That is a very compelling argument! So I will continue to tinker with my ideas, but later on I will switch to cards that has what I need already built so that I just have to connect them together. It will be great!
Since I ordered lithium batteries last week I’ve been researching what I need to get them to work on my boat, apart from the charger-inverter that I already have and the gizmos to get all that running. I’ve been researching battery monitoring systems, or BMS, that can handle my little pack of four cells. One that I really like is the REC ABMS and I might even get one. What I like about it is that it is made for four cells, and if I later decide to get four more I can just add another BMS, it has active balancing which means that it not only “bleed” the batteries while charging (and thus wasting energy and getting hot) but it will even balance the cells between each other when connected as a pack. So in theory the pack should get balanced as soon as the BMS detects that it is in inbalance.
What do I mean with an inbalanced pack? Well, it is a known fact that when having multiple cells making up a battery sometimes they doesn’t charge/discharge at the exact same rate, so after a while you get cells with different voltage, which isn’t optimal. So by balancing the BMS will transfer some energy from one battery to another to make sure that they are even. But I will write more about how I will set up my electrical system later, and most likely do a video of when I install them, as well as when I replace all the cabling in the boat since it is in a sub-par state.
I also spent the weekend looking for solutions to charge the battery bank with the engine, since the alternator is set to charge lead-acid batteries, rather than LiFePO4 batteries. I have found two promising products, the first one is Nordkyn Electronics VRC-200 Charge Reference Controller that a person in New Zeeland is building and selling. It is specifically made for the engine and alternator that I have, so it feels like a great match. But the home page looks a bit outdated and it was out of stock, so I sent him an email to inquire the state of things. He replied today that the VRC-200 is a relatively new design and that he’s been busy with other things lately so he haven’t had time to restock. This is obviously a warning signal, if there is some issues with it there might not be anyone there to help. We’ll see what happens, since I replied and asked if he were to start any production soon. And I just got a reply from him while writing this! Seems as if he wants to get the production running again, but there is no date as of now, but he would keep me informed.
Another product that does the same thing, as far as I could see, is the Wakespeed W500 Advanced Alternator Regulator and it also have cam bus connection, that can be nice, if it means that I can connect it to the BMS and potentially the charger-inverter as well. I will continue to dig into this issue, and see where I land in the end. I even had a person approach me from Facebook that is making a product like these and had some card that he wanted me to beta-test. We’ll see which way I will go, I need to know more before I decide.
So, what is the problem they are solving? Well, lead-acid batteries have a very different charging curve than lithium batteries. Mainly that they normally have three phases: bulk, absorption and float. They are, simplified, three different ways that the battery is charged. Bulk is where the current is constant and the voltage is increased, absorption when the voltage is constant and the current is ramped down and finally the float stage is when the battery is considered nearly full and the charge is at a lower voltage and current.
A LiFePO4 battery doesn’t have these phases, at all. It just gobbles down whatever current you are pushing to it. The beauty of a lithium battery is that it both deliver and accepts high currents and the voltage is quite constant. But if the voltage gets too high or too low it can be damaging the battery. So it is required to cut the charge as soon as the battery is considered full, when that is is obviously up for debate currently, but somewhere between 3.4-3.65V per cell is a good span, so 13.6-14.6V for the whole battery. Trying to push in more current at that time is not a good thing, so the alternator needs to be turned off.
But the alternator is running whenever the engine is running! Well, yes. But, without getting into too much technicalities (I’m afraid I already lost half of you reading this already), it can be controlled. Normally there is such a controller built into the alternator, as in my case, and it is not adjustable. It expects a lead-acid battery when charging, and will do all three phases no matter what. So, what to do? The first intuitive answer would be to put a switch that can disconnect the battery from the alternator when the battery is full, but that is a very good way to assure that the alternator dies a gruesome and painful death, since it has charged coils that suddenly doesn’t have anywhere to put this charge, and thus sends it back, blowing up the regulator. Oops… There is a better way, by having an external regulator instead that can turn off the field charge. But as I said, I have an alternator that has a built in regulator. It can be replaced, but it is pretty much like doing a heart transplant (okay, maybe not that hard, but it is some steps to go through). The third alternative is to make the alternator believe that it has a led-acid battery that it is charging. That is pretty much what the VRC-200 and W500 do, if I understand them correctly, give or take.
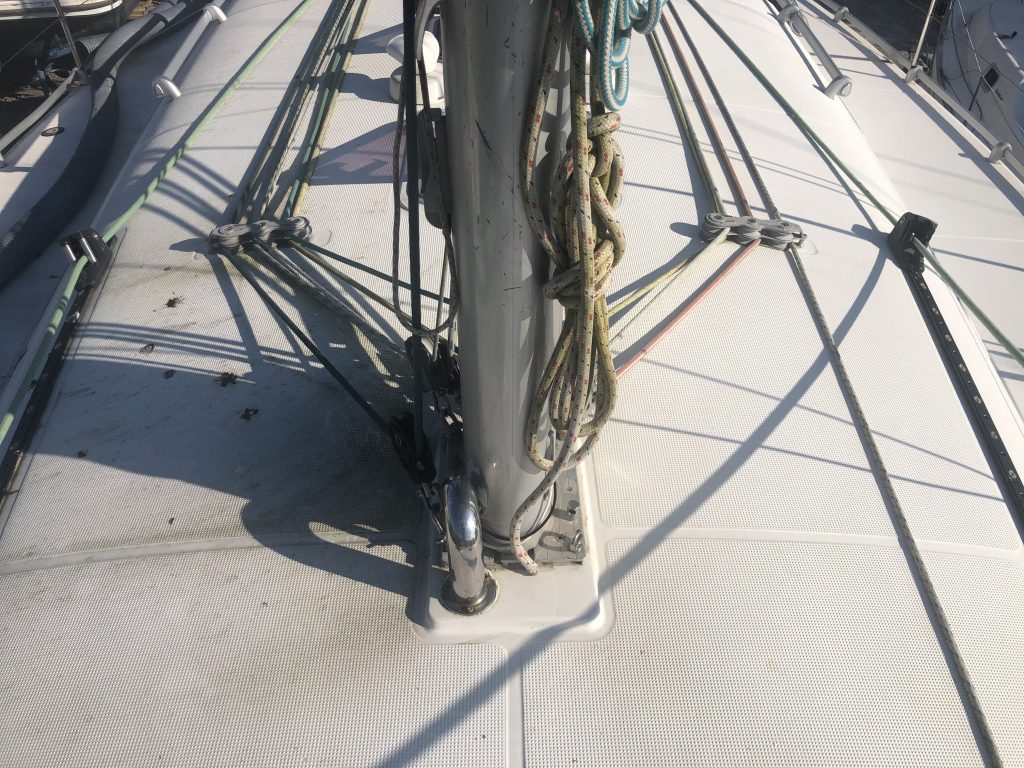
So, now you know a little more what I do when I do research! But that is not all that I’ve done. Today I washed the deck too. Well… most of port side of the boat anyway. Yes, I know, why not do all? Well, better done than perfect really. The bucket was empty, my back felt as if I shouldn’t expose it too much more to the sun and I was a bit tired. So… it got done, as far as I got. Best thing is that I highly doubt that anyone will come and rob me of the joy to do the rest of the deck. The really dirty part. The bird toilet part of the deck.
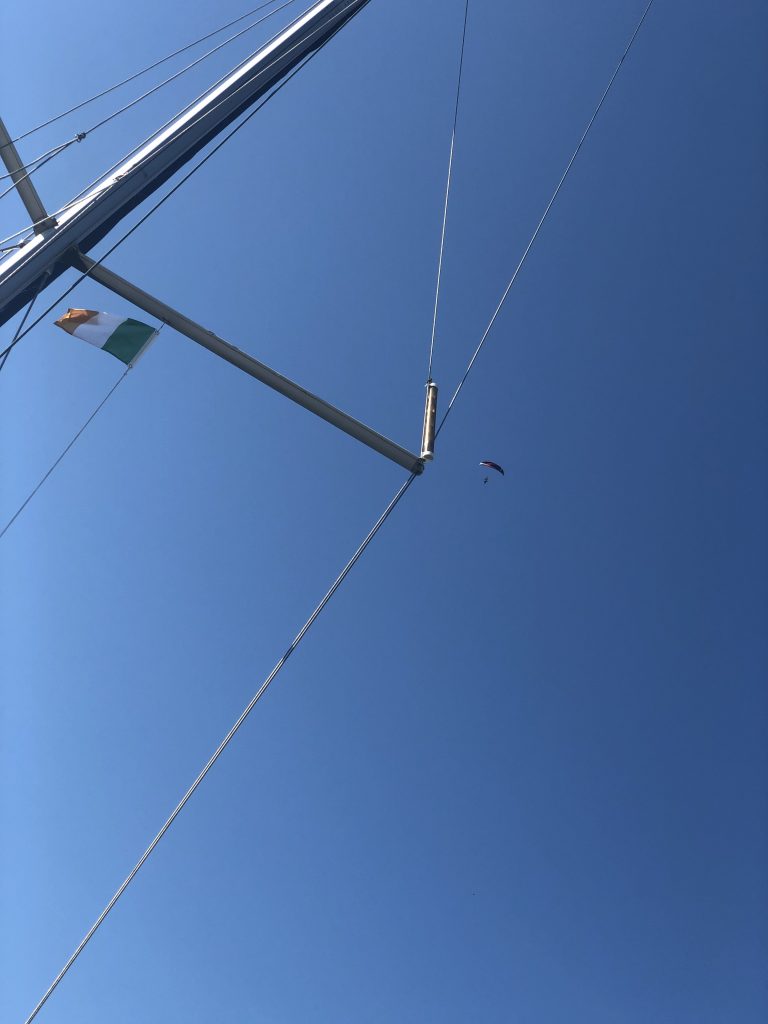
I had a wonderful dinner in the sun as well today, it just has been such a fantastic day! And when I was philosophing away after I was done, I heard some sound above me, and I saw this paraglider above the boat yard. That’s really cool! Oh, yes! I also hoisted the courtesy flag for Ireland. I mean, it was time for that.
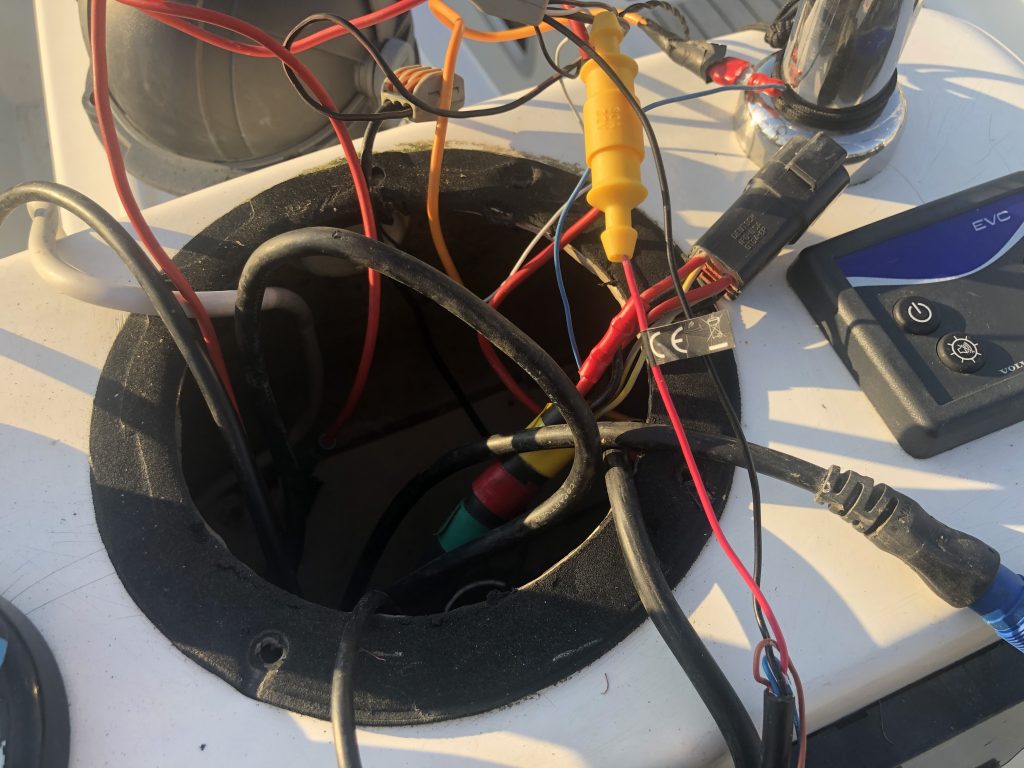
After dinner and some planning for a possible new cockpit table I wanted to understand the electrical connections of the instruments at the helm, and started to pick apart the helm station.
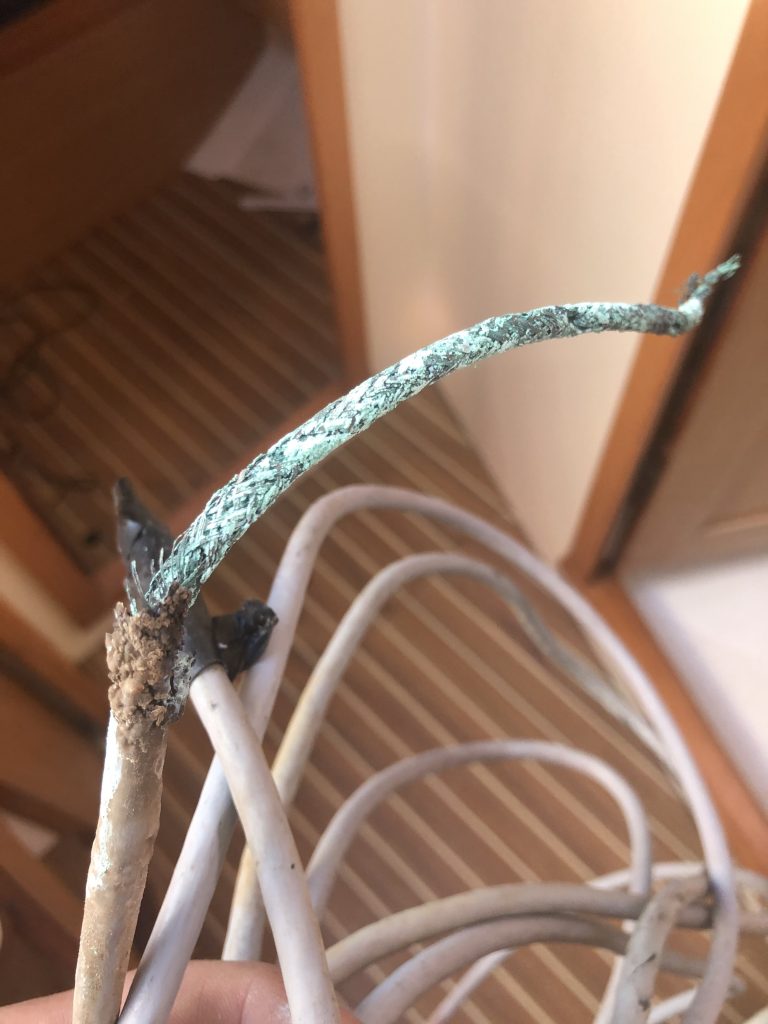
While doing that I realized that one cable going up through the cockpit sole (sole is the name of the floor in a boat) that I left down below to investigate where it might have been connected wasn’t even present in the helm station. So I decided to give it a good yank to see if I could get it to pull out. And yes it did. And wow how it looked! It was a shielded cable, but the shield was all exposed and it was totally corroded away. I guess I found out why they disconnected the cable at least. While continuing to pry and prod in the helm station I found another cable in there that wasn’t connected. It was ground cable and I already had one working in there, so I pulled that one too. Or so I thought. I accidentally pulled the one that was in use. Sigh. And, yeah, the other one almost got pulled out too. So now I have no ground wire in the helm. Great.
Tomorrow I will try to pick apart the rest of the helm station, for two reasons:
- Get the ground back up in the helm station
- Fix the rust of the backing mount under the cockpit sole
It is not a beautiful sight, to be fair, and it has been rusting for some time so there is long streaks of rust on the bulkhead below. It has to be fixed. And while I’m at it I can hopefully seal the helm station so that it won’t rust in the future. We’ll see.
Sorry about the long and technical text, I didn’t feel that I did much this weekend so I didn’t write anything then, but it seems as if I’ve done some things none the less.
Stay safe!