Well, as you can see in the post picture it wasn’t about grinding the rudder or not. I have had a somewhat odd rust leak in the rudder, and I had to inspect it. With a sander.
But as I sat down next to the rudder and sanded away the anti-fouling I started to notice a bulge at the tip of the rudder. A rather prominent bulge even, as if someone had repaired the rudder before, but not removing enough material so that the repair would blend with the previous form.
This was pretty much expected. I mean, Away has a history of being a charter boat so the main rule has been No One Cares And All Fixes Has To Be Quick. So I gave it a thought, should I do it the easy way, or The Right Way™?
Yeah, you already guessed it, the picture tells it too. So I started sanding. And sanding. And sanding. When the second battery died I realized I had to take stronger action. Either I’d go down to 40 grit paper from my current 80 grit, or… oh, yeah… time to bring out the grinder!
I’ve cut some fiberglass earlier with the grinder using a cut disc, but also thinned out the fiberglass with the grinder disc so I knew I was in for a ride. I soon noticed that the amount of fiberglass removed was pretty much linear to how much batteries I used. It just took 1/10th of the time with the grinder. So, yeah, it was a good choice.
What I noticed when I initially was sanding down the gelcoat and then the fiberglass was that there was multiple layers of gelcoat, some which was glassed over by the next repair. Which in an ideal world is just fine, since gelcoat is epoxi based. The only issue was that the innermost layer of gelcoat wasn’t adhered well to the fiberglass. So I wanted to remove all the gelcoat, sealer, fairing compound and fiberglass that was on top of that layer to make sure everything was sealed well and wouldn’t allow any water into the rudder.
So I grinded away with the mighty angel grinder, being happy that it seemed to work so well. After a while though I noticed that not all fiberglass that I managed to unveil was the classic yellowish color, but a much darker color. First, since I know that the boat is reinforced with some high-tech carbon fiber I thought it was it, but I reasoned long and well with myself that it would be a very silly place to put carbon in, since carbon is strong, but not that impact resistant. Why put carbon in an exposed position to be hit, I thought, maybe it is some sales pitch thing that they have done without discussing it with the engineers?
Well, it wasn’t carbon.
After some more grinding I noticed that the fiberglass was flexing a bit when I pushed the grinder at it. Even pushing it with my finger flexed it. A void. So, what to do? Well, It can’t be big, I argued and put the grinding disc at it, which immediately broke through and revealed the void. But how was this possible? The rudder was strong and when tapping on it it sounded really solid. Except around the hole I just had made. And then some. The entire dark area of the fiberglass sounded hollow.
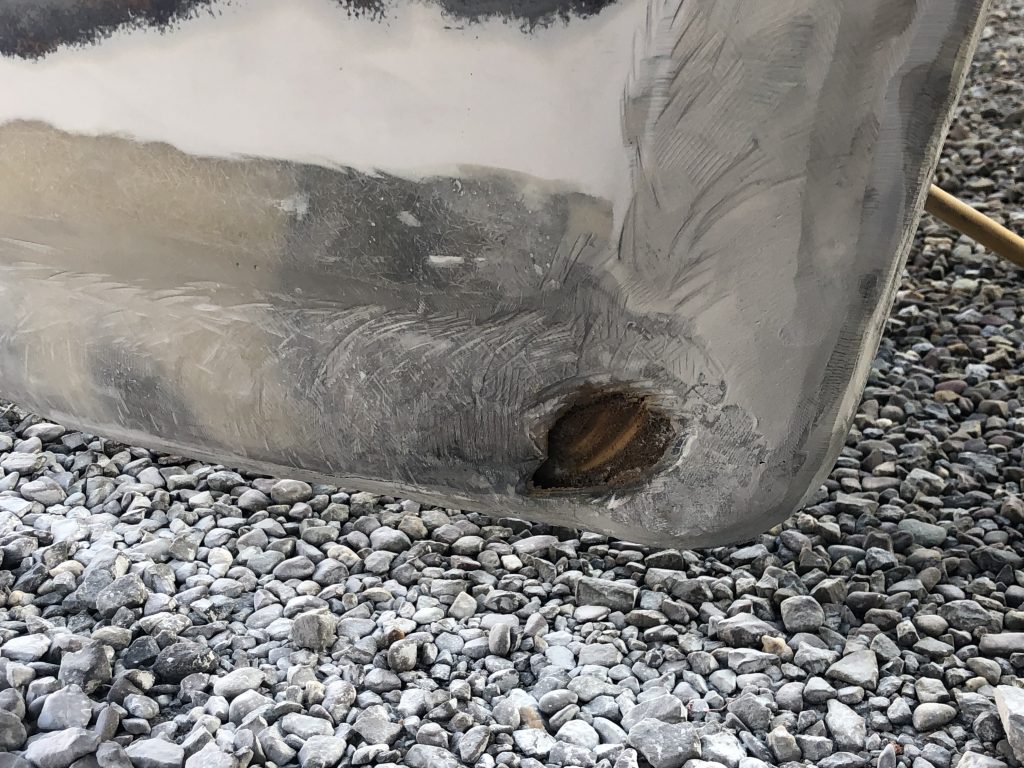
I took a piece of cable wrap that I found on the ground in all the gravel that I was lying on and pushed it in between the fiberglass and that material that initially looked like rust it disappeared in almost five centimeters, or almost all the way that the fiberglass was darker. The core material that looked like rust was later tested using the grinder and it seemed more wood-like, maybe hardboard..? I don’t know…
So, I got a hole in the rudder that I don’t know what to do with. The obvious answer would be to grind it all away and seal it properly, but is it worth it and will I be able to succeed? I have never laid up fiberglass and to do it up-side-down has been a challenge for those that I’ve followed doing it on YouTube. I need to talk to the people at the yard tomorrow. I’m mostly afraid that they will tell me that it was stupid to grind all that fiberglass away and that I should have followed the others example and just wrap a few more layers of glass and be done with it.
So, I’m back to…
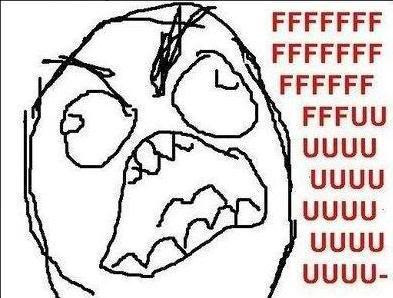